An Intelligent Manufacturing System for Injection Molding
Keywords:
PIM, industry 4.0, IoT, big data, cloud computing, IMS, BPNN, modified PSO-GAAbstract
In recent years, the great trends of industry 4.0, internet of things (IoT), big data analytics, and cloud computing, the design and development of plastic injection molding (PIM) products has been more requested to achieve the requirements of light, thin, short, small, multi-function, high-precision, energy-saving, and obliged to fulfill a large number of customized production. To tackle this arduous challenge, effectively developing a novel PIM intelligent manufacturing system will play a crucial role. The aim of the proposed study is to carry on building an intelligent manufacturing system (IMS) for PIM industry, which is composed of three subsystems: a multiple response optimization systems of PIM, a database management system of process parameters, and a PIM real-time monitoring and control system. Firstly, the multiple response optimization systems present an intelligent optimization system to find optimal process parameters of multiple quality characteristics in the PIM process. Secondly, the database management system allows for saving the experimental data, PIM process parameter settings and quality goals. The third is a PIM real-time monitoring and control system, which establishes a graphic monitoring and control interface to real-time monitor the parameters of PIM machine and the optimal process parameter settings. The proposed PIM intelligent manufacturing systems enable the functions of real-time monitoring, process parameter optimization and database management, which can assure better PIM product quality and yield rate, effectively reduce the manufacturing cost, and promote the competition of the PIM industry in the future.References
S. Wang, J. Wan, D. Zhang, D. Li, and C. Zhang, “Towards smart factory for industry 4.0: a self-organized multi-agent system with big data based feedback and coordination,” Computer Networks, vol. 101, no. 4, pp. 158-168, 2016.
A. Boboli, J. Okamoto, M. S. Tsuzuki, T. C. Martins, P. E. Miyagi, and F. Junqueira, “Intelligent manufacturing system configuration and optimization considering mobile robots, multi-functional machines and human operators: new facilities and challenge for industrial engineering,” International Federation of Automatic Control-Papers On Line, vol. 48, no. 3, pp. 1912-1917, 2015.
M. Hermann, T. Pentek, and B. Otto, “Design principles for industrie 4.0 scenarios,” 49th Hawaii International Conf. System Sciences (HICSS), IEEE Press, January 2016, pp. 3928-3937.
H. Kagermann, Recommendations for implementing the strategic initiative INDUSTRIE 4.0, National Academy of Science and Engineering, Berlin, Forschungsunion, 2013.
E. A. Lee, “Cyber physical systems: design challenges,” 11th IEEE Symposium Object Oriented Real-time Distributed Computing, May 2008, pp. 363-369.
H. K. Agermann and W. D. Lukas, “Industrie 4.0: mit dem internet der dinge auf dem weg zur 4. industriellen revolution,” https://goo.gl/7c4l2w, April 13, 2014.
P. Leitão, N. Rodrigues, J. Barbosa, C. Turrin, and A. Pagani, “Intelligent products: The grace experience,” Control Engineering Practice, vol. 42, pp. 95-105, 2015.
P. Pujo, N. Broissin, and F. Ounnar, “PROSIS: An isoarchic structure for HMS control,” Engineering Applications of Artificial Intelligence, vol. 22, no. 7, pp. 1034-1045, 2009.
V. Mařík, A. Schirrmann, D. Trentesaux, and P. Vrba, “Industrial applications of holonic and multi-agent systems,” 7th International Conf. Industrial Applications of Holonic and Multi-Agent Systems, September 2015.
N. Danišová, K. Velšek, and P. Košťál, “Automated tool changing system in the intelligent manufacturing and assembly cell,” International Symposium on Computing, Communication, and Control, October 2009, pp. 1-8.
Š. Horváth, E. Hrušková, and A. Mudriková, “Areas in flexible manufacturing-assembly cell,” Annals of Faculty Engineering Hunedoara-Journal of engineering, vol. 6, no. 3, pp. 123-127, 2008.
P. Leitão, “Agent-based distributed manufacturing control: a state-of-the-art survey,” Engineering Applications of Artificial Intelligence, vol. 22, no. 7, pp. 979-991, 2009.
H. Zhang, D. Tang, T. Huang, and C. Xu, “An agent based intelligent distributed control paradigm for manufacturing systems,” International Federation of Automatic Control-Papers On Line, vol. 49, no. 12, pp. 1549-1554, 2016.
J. Wang, L. Zhang, L. Duan, and R. X. Gao, “A new paradigm of cloud-based predictive maintenance for intelligent manufacturing,” Journal of Intelligent Manufacturing, vol. 28, no. 5, pp. 1125-1137, 2017.
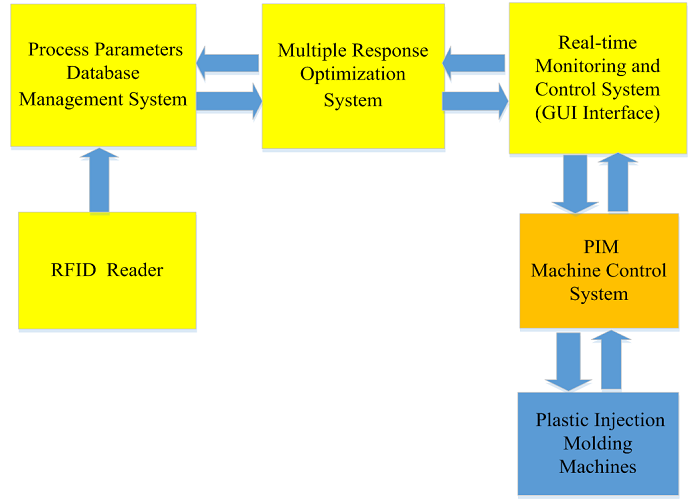
Published
How to Cite
Issue
Section
License
Submission of a manuscript implies: that the work described has not been published before that it is not under consideration for publication elsewhere; that if and when the manuscript is accepted for publication. Authors can retain copyright of their article with no restrictions. Also, author can post the final, peer-reviewed manuscript version (postprint) to any repository or website.
Since Oct. 01, 2015, PETI will publish new articles with Creative Commons Attribution Non-Commercial License, under The Creative Commons Attribution Non-Commercial 4.0 International (CC BY-NC 4.0) License.
The Creative Commons Attribution Non-Commercial (CC-BY-NC) License permits use, distribution and reproduction in any medium, provided the original work is properly cited and is not used for commercial purposes