Performance Characterization of Surface Quality and Tool Wear of Wet/Dry Drilling on Steels by Using Coated Drill Bits
Keywords:
drilling, coating, surface roughness, tool wearAbstract
The creation of holes by the drilling operation is a normal process which we were followed from the earlier days. Especially the drill bits’ usage is an Important consideration among the different drilling operations. Here we considered the coated form of drill bits for the purpose of improving the surface quality and to overcome the tool wear by the particulate deposition over the surface of the specimen. The drilling features are to find out over the specimen EN 8 Alloy steel and mild steel which are experimentally verified. In the view of differentiating the eminence of surface roughness and tool wear an appearance of Alloy steel and mild steel specimens, the wet and dry conditioned drilling operations are performed by the manifestation of coolants. The importance of Pertura and Latuma tool coated drill bits developed by the Physical Vapour Deposition (PVD) method are used for this operation. Based on the drilling conditions whether usage or non-usage of coolants is majorly influenced on surface roughness, and the tool coatings are politely influenced on the surface roughness of each specimen have been found out. Likewise, the tool coatings and the rotational speed influenced more on machining time has been recognized. Tool wear patterns are categorized and compared with the simulation data of drilling in Deform 3D. Effective stress is identified and related to the value of surface coarseness in both conditions of drilling on different steel specimens.
References
J. Pradeep Kumar and P. Packiaraj, “Effect of drilling parameters on surface roughness, tool wear, material removal rate, and hole diameter error in drilling of ohns,” International Journal of Advanced Engineering Research and Studies, vol. 1, no. 3, pp. 150-154, June 2012.
B. V. Kavada, A. B. Pandey, M.V. Tadavi, and H. C. Jakharia, “A review paper on effects of drilling on glass fiber reinforced plastic,” ICIAME 2014, Procedia Technology, vol. 14, pp. 457-464, August 2014.
M. A. J. Bosco, K. Palanikumar, B. Durga Prasad, and A. Velayudham, “Influence of machining parameters on delamination in drilling of GFRP- armour steel sandwich composites,” NUiCONE 2012, Procedia Engineering, vol. 51, pp. 758-763, January 2013.
E. Bahce and C. Ozel, “Experimental investigation of the effect of machining parameters on the surface roughness and the formation of built up edge (BUE) in the Drilling of Al 5005,” Tribology in Engineering, Hasim Pihtili, IntechOpen, Chapter 2, pp. 15-28, May 2013.
Cicek A. Kıvak, T. Samtas, G. Adem Cicek, Turgay Kıvak, and Gurcan Samtas, “Application of taguchi method for surface roughness and roundness error in drilling of AISI 316 stainless steel,” Journal of Mechanical Engineering, vol. 58, no. 3, pp. 165-174, January 2012.
N. S. Mohan and S. M. Kulkarni, “Influence of drilling parameters on torque during drilling of GFRP composites using response surface methodology,” The 2nd International Joint Conference on Science and Technology (IJCST) pp. 1-7, September 2017.
A. A. Thakre, “Modelling of burr size in drilling of aluminium silicon carbide composites using response surface methodology,” An International Journal of Engineering Science and Technology, vol. 19, pp. 1199-1205, March 2016..
X. Chen, L. Xie, X. Nan, J. Tian, and W. Zhao, “Experimental study of small hole drilling characteristics of SiCp/Al composites,” Procedia CIRP, vol. 46, March 2016 pp. 319-322.
Puneeth. V and Smitha. B, “Studies on tool life and cutting forces for drilling operation using uncoated and coated HSS tool,” International Research Journal of Engineering and Technology (IRJET), vol. 4, no. 6, pp. 1949-1954, June 2017.
B. Pradeep Kumar, Dr. N. V. N. Indra Kiran, and S. Phani Kumar. “Effect of cutting parameters in drilling of EN8 (080M40) carbon steel to obtain maximum MRR and minimum temperature by using RSM (under dry condition)” International Journal of Engineering and Management, vol. 7, no. 2, pp. 533-539, April 2017.
R. Sreenivasulu and C. S. Rao, “Effect of drilling parameters on thrust force and torque during drilling of aluminium 6061 alloy based on taguchi design of experiments,” Journal of Mechanical Engineering, no. 46, pp. 41-48, December 2016.
D. Shetty S, N. Shetty, A. Rajat, G. Shetty, and P. Patil, “Characterization of machining parameters on thrust force and surface roughness in drilling of 40-60 Wt. % BD CFRP composite,” International Journal of Applied Engineering Research, vol. 12, no. 16, pp. 5570-5577, September 2017.
N. Tosun, “Determination of optimum parameters for multi-performance characteristics in drilling by using grey relational analysis,” International Journal of Advanced Manufacturing Technology, vol. 28, pp. 450-455, March 2006.
D. Arola and C.L. Williams, “Estimating the fatigue stress concentration factor of machined surfaces,” International Journal of Fatigue, vol. 24, pp. 923-930, September 2002.
J. M. Dasch, C. C. Ang, C. A. Wong, Y. T. Cheng, A. M. Weiner, L. C. Lev, and E. Konca, “A comparison of five categories of carbon-based tool coatings for dry drilling of aluminum,” Surface and Coatings Technology, vol. 200, pp. 2970-2977, February 2006.
X. Wang, X. Shen, C. Zeng, and F. Sun, “Combined influences of tool shape and as-deposited diamond film on cutting performance of drills for CFRP machining,” Surface and Coatings Technology, vol. 347, pp. 390-397, May 2018.
D. U. Braga, A. E. Diniz, G. W. A. Miranda, and N. L. Coppini, “Using a minimum quantity of lubricant (MQL) and a diamond coated tool in the drilling of aluminum-silicon alloys,” Journal of Materials Processing Technology, vol. 122, pp. 127-138, March 2002.
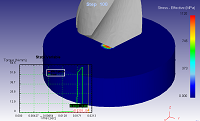
Published
How to Cite
Issue
Section
License
Submission of a manuscript implies: that the work described has not been published before that it is not under consideration for publication elsewhere; that if and when the manuscript is accepted for publication. Authors can retain copyright of their article with no restrictions. Also, author can post the final, peer-reviewed manuscript version (postprint) to any repository or website.
Since Oct. 01, 2015, PETI will publish new articles with Creative Commons Attribution Non-Commercial License, under The Creative Commons Attribution Non-Commercial 4.0 International (CC BY-NC 4.0) License.
The Creative Commons Attribution Non-Commercial (CC-BY-NC) License permits use, distribution and reproduction in any medium, provided the original work is properly cited and is not used for commercial purposes