Development of a Dryer with a Heat Exchanger to Recover Energy for Drying Agricultural Produce
DOI:
https://doi.org/10.46604/peti.2018.2815Keywords:
drying, heat exchanger, energy, agricultural produceAbstract
The purpose of this study was to investigate the effect of a heat recovery by guiding the exhaust air through a heat exchanger in a hot air dryer. The temperature of inlet air could be increased by the developed heat recovery device to achieve energy saving. Experimental results indicated that the heat recovery device could increase the inlet fresh temperature 11℃, the effectiveness ratio of the heat exchanger was up to 70-80%, and heating efficiency of the heater was 50% through the analysis of inlet and outlet temperature, airflow rate as well as fuel consumption of the heater. In addition, the maximum temperature difference in the drying chamber was in the range of 0.6-1.2℃, indicating that the airflow in the drying was uniform, thus the uniform quality of agricultural produce could be obtained. In order to analyse the optimum operation conditions, the effect of fan speed on the temperature and airflow distribution was investigated in the drying system. The results showed that the optimum fan speed should be faster during start-up period and lower during a steady stage.
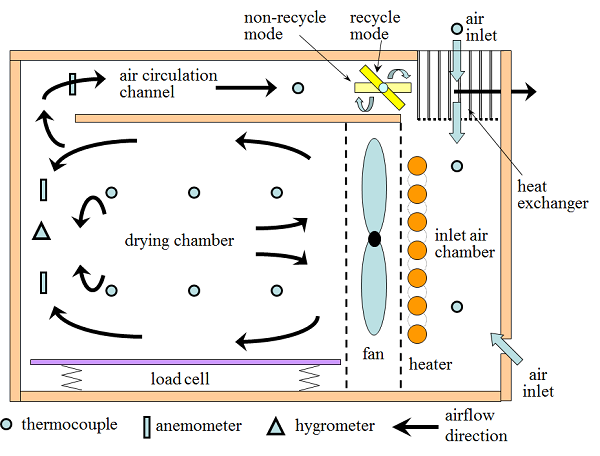
Published
How to Cite
Issue
Section
License
Submission of a manuscript implies: that the work described has not been published before that it is not under consideration for publication elsewhere; that if and when the manuscript is accepted for publication. Authors can retain copyright of their article with no restrictions. Also, author can post the final, peer-reviewed manuscript version (postprint) to any repository or website.
Since Oct. 01, 2015, PETI will publish new articles with Creative Commons Attribution Non-Commercial License, under The Creative Commons Attribution Non-Commercial 4.0 International (CC BY-NC 4.0) License.
The Creative Commons Attribution Non-Commercial (CC-BY-NC) License permits use, distribution and reproduction in any medium, provided the original work is properly cited and is not used for commercial purposes