A Modified Exponential Model for Predicting the Fatigue Crack Growth Rate in a Pipeline Steel Under Pure Bending
DOI:
https://doi.org/10.46604/aiti.2024.14372Keywords:
exponential function, specific growth rate, fatigue crack, stress intensity factor, SDG 9Abstract
The present work proposes a fatigue crack growth rate (FCGR) model for steel pipelines subjected to sinusoidal loading using a modified exponential function. The modification in the exponential function is made for the non-dimensional parameter using the stress intensity range (ΔK) as the crack driving force. The acceptable values of ΔK for FCGR in stage-I ranged between 17.45-20.46 MPa√m, between 20.46-21.41 MPa√m for stage-II, and between 21.41-21.98 MPa√m for stage-III. A new correlation is also developed between the specific growth rate and the non-dimensional number. The modified exponential function predicted the FCGR within the acceptable values for all three stages in the radial direction. It shows the best performance for stage-I of FCGR and the lowest for stage-III. The microstructure envisages shallowed microvoids, while the striations and secondary cracks are mostly perpendicular to the FCG direction.
References
J. Wanjun, W. Jinfu, N. Cunhou, and P. Xiaofei, “Application of Austenitic Stainless Steel Pipe in Petrochemical Units,” Petroleum Refinery Engineering, vol. 53, no. 9. pp. 35-37, 2023.
S. Vishnuvardhan et al., “Fatigue Ratcheting Studies on TP304 LN Stainless Steel Straight Pipes,” Procedia Engineering, vol. 2, no. 1, pp. 2209-2218, 2010.
A. B. Radwan, A. M. Abdullah, H. J. Roven, A. M. Mohamed, and S. K. Mobbassar Hassan, “Failure Analysis of 316L Air Cooler Stainless Steel Tube in a Natural Gas Production Field,” International Journal of Electrochemical Science, vol. 10, no. 9, pp. 7606-7621, 2015.
M. Puiggali, S. Rousserie, and M. Touzet, “Fatigue Crack Initiation on Low-Carbon Steel Pipes in a Near-Neutral-pH Environment Under Potential Control Conditions,” Corrosion, vol. 58, no. 11, 2002.
X. Guo, D. Zhang, and J. Zhang, “Detection of Fatigue-Induced Microcracks in a Pipe by Using Time-Reversed Nonlinear Guided Waves: A Three-Dimensional Model Study,” Ultrasonics, vol. 52, no. 7, pp. 912-919, 2012.
A. H. Noroozi, G. Glinka, and S. Lambert, “A Study of the Stress Ratio Effects on Fatigue Crack Growth Using the Unified Two-Parameter Fatigue Crack Growth Driving Force,” International Journal of Fatigue, vol. 29, no. 9-11, pp. 1616-1633, 2007.
A. H. Noroozi, G. Glinka, and S. Lambert, “Prediction of Fatigue Crack Growth under Constant Amplitude Loading and a Single Overload Based on Elasto-Plastic Crack Tip Stresses and Strains,” Engineering Fracture Mechanics, vol. 75, no. 2, pp. 188-206, 2008.
P. K. Singh et al., “Fatigue Studies on Carbon Steel Piping Materials and Components: Indian PHWRs,” Nuclear Engineering and Design, vol. 238, no. 4, pp. 801-813, 2008.
T. Hassan, M. Rahman, and S. Bari, “Low-Cycle Fatigue and Ratcheting Responses of Elbow Piping Components,” Journal of Pressure Vessel Technology, vol. 137, no. 3, article no. 031010, 2015.
H. Shirazi, S. Wang, W. Chen, and R. Eadie, “Pipeline Circumferential Corrosion Fatigue Failure under the Influence of Bending Residual Stress in the Near-Neutral pH Environment,” Engineering Failure Analysis, vol. 166, pp. 108887, 2024.
W. Liang, M. Lou, C. Zhang, D. Zhao, D. Yang, and Y. Wang, “Experimental Investigation and Phenomenological Modeling of Fatigue Crack Growth in X80 Pipeline Steel under Random Loading,” International Journal of Fatigue, vol. 182, pp. 108169, 2024.
Z. Lin et al., “The Dependence of Fatigue Property on Applied Stress in X80 Pipeline Steel Notched Specimens in Hydrogen Gas Environment,” International Journal of Fatigue, vol. 183, pp. 108222, 2024.
T. An, H. Peng, P. Bai, S. Zheng, X. Wen, and L. Zhang, “Influence of Hydrogen Pressure on Fatigue Properties of X80 Pipeline Steel,” International Journal of Hydrogen Energy, vol. 42, no. 23, pp. 15669-15678, 2017.
O. Fatoba and R. Akid, “Low Cycle Fatigue Behaviour of API 5L X65 Pipeline Steel at Room Temperature,” Procedia Engineering, vol. 74, pp. 279-286, 2014.
Y. Jiang and M. Chen, “Researches on the Fatigue Crack Propagation of Pipeline Steel,” Energy Procedia, vol. 14, pp. 524-528, 2012.
M. A. Mohtadi-Bonab, M. Eskandari, H. Ghaednia, and S. Das, “Effect of Microstructural Parameters on Fatigue Crack Propagation in an API X65 Pipeline Steel,” Journal of Materials Engineering and Performance, vol. 25, no. 11, pp. 4933-4940, 2016.
M. A. Mohtadi-Bonab, M. Eskandari, M. Sanayei, and S. Das, “Microstructural Aspects of Intergranular and Transgranular Crack Propagation in an API X65 Steel Pipeline Related to Fatigue Failure,” Engineering Failure Analysis, vol. 94, pp. 214-225, 2018.
J. A. Ronevich, B. P. Somerday, and C. W. San Marchi, “Effects of Microstructure Banding on Hydrogen-Assisted Fatigue Crack Growth in X65 Pipeline Steels,” International Journal of Fatigue, vol. 82, pp. 497-504, 2016.
A. J. Slifka et al., “The Effect of Microstructure on the Hydrogen-Assisted Fatigue of Pipeline Steels,” Proceedings of American Society of Mechanical Engineers, Pressure Vessels and Piping Division (Publication) PVP, vol. 6, ASME Press, 2013.
V. Igwemezie, A. Mehmanparast, and F. Brennan, “The Influence of Microstructure on the Fatigue Crack Growth Rate in Marine Steels in the Paris Region,” Fatigue & Fracture of Engineering Materials & Structures, vol. 43, no. 10, pp. 2416-2440, 2020.
V. K. Sahu, P. K. Ray, and B. B. Verma, “Experimental Fatigue Crack Growth Analysis and Modelling in Part-Through Circumferentially Pre-Cracked Pipes under Pure Bending Load,” Fatigue & Fracture of Engineering Materials & Structures, vol. 40, no. 7, pp. 1154-1163, 2017.
P. Kumar, H. Patel, P. K. Ray, B. B.Verma, "Calibration of COD Gauge and Determination of Crack Profile for Prediction of Through the Thickness Fatigue Crack Growth in Pipes Using Exponential Function," Mechanics, Materials Science & Engineering, no. 9, 2016.
P. Kumar, V. K. Sahu, P. K. Ray, B. B. Verma, "Modelling of Fatigue Crack Propagation in Part-Through Cracked Pipes Using Gamma Function," Mechanics, Materials Science & Engineering, no. 9, 2016.
P. Kumar, M. E. Makhatha, S. Sengupta, and A. K. Dutt, “Prediction of the Propagation of Fatigue Cracks in Part-Through Cracked Pipes with CASCA and FRANC2D,” Transactions of the Indian Institute of Metals, vol. 73, no. 6, pp. 1417-1420, 2020.
S. Al Laham and S. I. Branch, Stress Intensity Factor and Limit Load Handbook, vol. 3. British Energy Generation Limited, Gloucester, UK, 1998.
A. Albedah, B. Bachir Bouiadjra, L. Aminallah, M. Es-Saheb, and F. Benyahia, “Numerical Analysis of the Effect of Thermal Residual Stresses on the Performances of Bonded Composite Repairs in Aircraft Structures,” Composites Part B: Engineering, vol. 42, no. 3, pp. 511-516, 2011.
T. L. Anderson, Fracture Mechanics: Fundamentals and Applications, 4th ed. Boca Raton, FL: CRC Press, 2017.
C. M. Roşca, Vâlcu ; Miriţoiu, “Fnk Model of Cracking Rate Calculus for a Variable Asymmetry Coefficient,” Acta Universitatis Cibiniensis, vol. 69, no. 1, pp. 72-81, 2017.
W. F. Gale and T. C. Totemeier, Eds., Smithells Metals Reference Book, 8th ed. Butterworth-Heinemann, 2003.
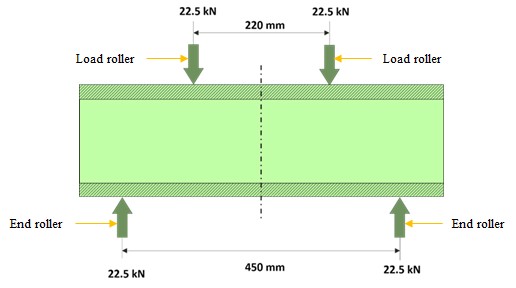
Published
How to Cite
Issue
Section
License
Copyright (c) 2025 Sergei Sherbakov, Pawan Kumar, Daria Podgayskaya, Pavel Poliakov, Vasilii Dobrianskii, Vishwanatha H M

This work is licensed under a Creative Commons Attribution-NonCommercial 4.0 International License.
Submission of a manuscript implies: that the work described has not been published before that it is not under consideration for publication elsewhere; that if and when the manuscript is accepted for publication. Authors can retain copyright in their articles with no restrictions. is accepted for publication. Authors can retain copyright of their article with no restrictions.
Since Jan. 01, 2019, AITI will publish new articles with Creative Commons Attribution Non-Commercial License, under The Creative Commons Attribution Non-Commercial 4.0 International (CC BY-NC 4.0) License.
The Creative Commons Attribution Non-Commercial (CC-BY-NC) License permits use, distribution and reproduction in any medium, provided the original work is properly cited and is not used for commercial purposes.