Effects of the Vibration Amplitude in Vibratory Stress Relief on the Fatigue Life of Structures
DOI:
https://doi.org/10.46604/aiti.2021.8714Keywords:
vibratory stress relief (VSR), residual stress, fatigue life, fatigue limit, vibration amplitudeAbstract
This research aims to investigate the effects of vibration amplitude in vibratory stress relief (VSR) on the fatigue strength of structures with residual stress. Experiments are carried out on specimens with residual stress generated by local heating. Flat specimens made of A36 steel are prepared to be suitable for setting up fatigue bending tests on a vibrating table. Several groups of samples are subjected to VSR at resonant frequencies with different acceleration amplitudes. The results show that VSR has an important influence on the residual stress and fatigue limit of steel specimens. The maximum residual stress in the samples is reduced about 73% when the amplitude of vibration acceleration is 57 m/s2. The VSR method can also improve the fatigue limit by up to 14% for steel samples with residual stress.
References
J. S. Robinson, M. S. Hossain, and C. E. Truman, “Residual Stresses in the Aluminum Alloy 2014A Subject to PAG Quenching and Vibratory Stress Relief,” The Journal of Strain Analysis for Engineering Design, in press.
Q. Wu, D. P. Li, and Y. D. Zhang, “Detecting Milling Deformation in 7075 Aluminum Alloy Aeronautical Monolithic Components Using the Quasi-Symmetric Machining Method,” Metals, vol. 6, no. 4, 80, April 2016.
M. J. Vardanjani, M. Ghayour, and R. M. Homami, “Analysis of the Vibrational Stress Relief for Reducing the Residual Stresses Caused by Machining,” Experimental Techniques, vol. 40, no. 2, pp. 705-713, April 2016.
H. Sasahara, “The Effect on Fatigue Life of Residual Stress and Surface Hardness Resulting from Different Cutting Conditions of 0.45% C Steel,” International Journal of Machine Tools and Manufacture, vol. 45, no. 2, pp. 131-136, February 2005.
M. Benedetti, V. Fontanari, P. Scardi, C. A. Ricardo, and M. Bandini, “Reverse Bending Fatigue of Shot Peened 7075-T651 Aluminum Alloy: The Role of Residual Stress Relaxation,” International Journal of Fatigue, vol. 31, no. 8-9, pp. 1225-1236, 2009.
M. S. Patil, R. R. Wayakole, and K. D. Sarode, “Vibratory Residual Stress Relief in Manufacturing—A Review”, International Journal of Engineering Sciences and Research Technology, vol. 6, no. 5, pp. 609-613, May 2017.
H. Song, H. Gao, Q. Wu, and Y. Zhang, “Effects of Segmented Thermal-Vibration Stress Relief Process on Residual Stresses, Mechanical Properties and Microstructures of Large 2219 Al Alloy Rings,” Journal of Alloys and Compounds, vol. 886, 161269, December 2021.
C. A. Walker, A. J. Waddell, and D. J. Johnston, “Vibratory Stress Relief—An Investigation of Underlying Process,” Proc. of the Institution of Mechanical Engineers, Part E: Journal of Process Mechanical Engineering, vol. 209, no. 1, pp. 51-58, February 1995.
G. Cai, Y. Huang, and Y. Huang, “Operating Principal of Vibratory Stress Relief Device Using Coupled Lateral-Torsional Resonance,” International Journal of Vibroengineering, vol. 19, no. 6, pp. 4083-4097, 2017.
M. C. Sun, Y. H. Sun, and R. K. Wang, “The Vibratory Stress Relief of a Marine Shafting of 35# Bar Steel,” Materials Letters, vol. 58, no. 3-4, pp. 299-303, January 2004.
D. Rao, J. Ge, and L. Chen, “Vibratory Stress Relief in Manufacturing the Rails of a Maglev System,” Journal of Manufacturing Science and Engineering, vol. 126, no. 2, pp. 388-391, May 2004.
D. Rao, D. Wang, L. Chen, and C. Ni, “The Effectiveness Evaluation of 314L Stainless Steel Vibratory Stress Relief by Dynamic Stress,” International Journal of Fatigue, vol. 29, no. 1, pp. 192-196, January 2007.
H. Gong, Y. Sun, Y. Liu, Y. Wu, Y. He, X. Sun, et al., “Effect of Vibration Stress Relief on the Shape Stability of Aluminum Alloy 7075 Thin-Walled Parts,” Metals, vol. 9, no. 1, 27, January 2019.
C. Walker, “A Theoretical Review of the Operation of Vibratory Stress Relief with Particular Reference to the Stabilization of Large-Scale Fabrications,” Proc. of the Institution of Mechanical Engineers, Part L: Journal of Materials: Design and Applications, vol. 225, no. 3, pp. 195-204, July 2011.
A. M. Fayrushin, R. R. Chernyatyeva, and D. N. Yakovleva, “The Effects of Vibration Treatment in the Process of Welding on the Structure of Metal of Seam Weld,” IOP Conference Series: Earth and Environmental Science, vol. 459, 062110, 2020.
H. Gao, S. Wu, Q. Wu, B. Li, Z. Gao, Y. Zhang, et al., “Experimental and Simulation Investigation on Thermal-Vibratory Stress Relief Process for 7075 Aluminum Alloy,” Materials and Design, vol. 195, 108954, October 2020.
D. X. Fang, F. H. Sun, Z. K. Gong, A. X. Jia, and Y. A. Qu, “Improving Fatigue Life of Welded Components by Vibratory Stress Relief Technique,” International Journal Experiment Mechanical, vol. 6, pp. 89-95, 1991.
A. Munsi, A. J. Waddell, and C. Walker, “The Influence of Vibratory Treatment on the Fatigue Life of Welds: A Comparison with Thermal Stress Relief,” Strain, vol. 37, no. 4, pp. 141-149, 2001.
D. Djuric, R. Vallant, K. Kerschbaumer, and N. Enzinger, “Vibration Stress Relief Treatment of Welded High-Strength Martensitic Steel,” Welding in the World, vol. 55, no. 1, pp. 86-93, 2011.
H. J. Gao, Y. D. Zhang, Q. Wu, and J. Song, “Experimental Investigation on the Fatigue Life of Ti-6Al-4V Treated by Vibratory Stress Relief,” Metals, vol. 7, no. 5, 158, May 2017.
J. Song and Y. Zhang, “Effect of Vibratory Stress Relief on Fatigue Life of Aluminum Alloy 7075-T651,” Advances in Mechanical Engineering, vol. 8, no. 6, pp. 1-9, 2016.
H. Gao, Y. Zhang, Q. Wua, J. Song, and K. Wen, “Fatigue Life of 7075-T651 Aluminum Alloy Treated with Vibratory Stress Relief,” International Journal of Fatigue, vol. 108, pp. 62-67, March 2018.
Standard Test Method for Determining Residual Stresses by the Hole-Drilling Strain-Gage Method, ASTM E837-13a, 2013.
M. Kuroda, A. Sakida, N. Oguma, M. Nakagawa, T. Matsumura, and T. Sakai, “Historical Review on Origin and Application to Metal Fatigue of Probit and Staircase Method and Their Future Prospects,” Journal of the Society of Materials Science, vol. 70, no. 3, pp. 221-228, March 2021.
C. Müller, M. Wächter, R. Masendorf, and A. Esderts, “Accuracy of Fatigue Limits Estimated by the Staircase Method Using Different Evaluation Techniques,” International Journal of Fatigue, vol. 100, pp. 296-307, July 2017.
H. Xue, R. R. Li, L. X. Wu, W. J. Peng, and J. Q. Huang, “The Fatigue Performance Evaluation of Pressure Vessel Steel Using Modified Staircase Method,” Advanced Materials Research, vol. 989, pp. 879-882, 2014.
I. M. W. Ekaputra, R. T. Dewa, G. D. Haryadi, and S. J. Kim, “Fatigue Strength Analysis of S34MnV Steel by Accelerated Staircase Test,” Open Engineering, vol. 10, no. 1, pp. 394-400, 2020.
International Council on Combustion Engines Working Group 4 (CIMAC WG4), “IACS UR M53, Appendix IV, Guidance for Evaluation of Fatigue Tests,” Report, October 16, 2009.
Strength Calculation and Testing: Methods of Fatigue Strength Behavior Calculation, GOST 25.504-82, 1982. (In Russian)
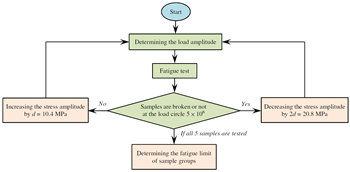
Published
How to Cite
Issue
Section
License
Submission of a manuscript implies: that the work described has not been published before that it is not under consideration for publication elsewhere; that if and when the manuscript is accepted for publication. Authors can retain copyright in their articles with no restrictions. is accepted for publication. Authors can retain copyright of their article with no restrictions.
Since Jan. 01, 2019, AITI will publish new articles with Creative Commons Attribution Non-Commercial License, under The Creative Commons Attribution Non-Commercial 4.0 International (CC BY-NC 4.0) License.
The Creative Commons Attribution Non-Commercial (CC-BY-NC) License permits use, distribution and reproduction in any medium, provided the original work is properly cited and is not used for commercial purposes.