Flexural Strength and Porosity of NaOH-Treated Maize Stalk Cellulose-Fibers-Reinforced Geopolymer Composites
DOI:
https://doi.org/10.46604/peti.2023.10285Keywords:
maize, cellulose, geopolymer, composite, characterization, calcined kaolinAbstract
This study characterizes the flexural strength and porosity of NaOH-treated maize stalk cellulose-fibers-reinforced geopolymer composites. Flexural strength tests are conducted, and the fracture surfaces of the composite and geopolymer powder are observed using a scanning electron microscope (SEM). Moreover, porosity analysis is also performed using Image J software from SEM images. The formation of geopolymer is confirmed using X-ray diffraction (XRD) and Fourier transform infrared (FTIR) analysis. The addition of 1.5 wt% of NaOH-treated maize stalk cellulose fibers improves flexural strength by 2.4 times. The results show that the main failure mechanisms, namely fiber breakage, fiber pullout, and debonding of the fiber and matrix, can increase flexural strength and reduce failures during service life. During the analysis for fiber and particle pullout, SEM images under 25^2 pixels of pore areas are not considered, and an average porosity of 36.7% is achieved.
References
K. Sankar and W. M. Kriven, “Potassium Geopolymer Reinforced with Alkali-Treated Fique,” Developments in Strategic Materials and Computational Design V: A Collection of Papers Presented at the 38th International Conference on Advanced Ceramics and Composites, vol. 35, pp. 61-78, December 2014.
T. Alomayri, F. U. A. Shaikh, and I. M. Low, “Synthesis and Mechanical Properties of Cotton Fabric Reinforced Geopolymer Composites,” Composites Part B: Engineering, vol.60, pp. 36-42, April 2014.
H. Assaedi, T. Alomayri, F. U.A.Shaikh. and I. M. Low, “Characterisation of Mechanical and Thermal Properties in Flax Fabric Reinforced Geopolymer Composites,” Journal of Advanced Ceramics, vol. 4, no. 4, pp. 272-281, December 2015.
C. Visvanathan and C. Chiemchaisri, “Management of Agricultural Wastes and Residues in Thailand: Wastes to Energy Approach,” http:/faculty.ait.ac.th/visu/wp-content/uploads/sites/7/2019/01/Agri-waste2energy-Thai.pdf, 2019.
T. Lin, D. Jia, P. He, and M. Wang, “Effects of Fibre Content on Mechanical Properties and Fracture Behaviour of Short Carbon Fibre Reinforced Geopolymer Matrix Composites,” Bulletin of Materials Science, vol. 32, no. 1, pp. 77-81, February 2009.
U. H. Heo, K. Sankar, W. M. Kriven, and S. S. Musil, “Rice Husk Ash as a Silica Source in a Geopolymer Formulation,” Developments in Strategic Materials and Computational Design V: A Collection of Papers Presented at the 38th International Conference on Advanced Ceramics and Composites, vol. 35, pp. 87-101, December 2014.
P. A. N. V. L. NarasimahSwamy, U. VenuGopal, and K. Prasanthi, “Experimental Study on Coir Fibre Reinforced Flyash Based Geopolymer Concrete with 12M and 10M Molar Activator,” International Journal of Civil Engineering and Technology, vol 8, no 4, pp. 2210-2216, April 2017.
A. Berzins, A. Morozovs, U. Gross, and J. Lejavs, “Mechanical Properties of Wood-Geopolymer Composite,”, 16th International Scientific Conference “Engineering for Rural Development”, pp. 1167- 1173, May 2017.
T. Alomayri, F. U. A. Shaikh, and I. M. Low, “Effect of Fabric Orientation on Mechanical Properties of Cotton Fabric Reinforced Geopolymer Composites,” Materials & Design, vol. 57, pp. 360-365, May 2014.
P. D. Jero and R. J. Kerans, “The Contribution of Interfacial Roughness to Sliding Friction of Ceramic Fibers in a Glass Matrix,” Scripta Metallurgica et Materialia, vol. 24, no. 12, pp. 2315-2318, December 1990.
R. J. Kerans, “Issues in the Control of Fiber-Matrix Interface Properties in Ceramic Composites,” Scripta Metallurgica et Materialia, vol. 31, no. 8, pp. 1079-1084, October 1994.
D. R. Mumm and K. T. Faber, “Interfacial Debonding and Sliding in Brittle-Matrix Composites Measured Using an Improved Fiber Pullout Technique,” Acta Metallurgica et Materialia, vol. 43, no. 3, pp. 1259-1270, March 1995.
F. F. Lange, W. C. Tu, and A. G. Evans, “Processing of Damage-Tolerant, Oxidation-Resistant Ceramic Matrix Composites by a Precursor Infiltration and Pyrolysis Method,” Materials Science and Engineering: A, vol. 195, pp. 145-150, June 1995.
F. W. Zok and C. G. Levi, “Mechanical Properties of Porous-Matrix Ceramic Composites,” Advanced Engineering Materials, vol. 3, no. 1-2, pp. 15-23, January 2001.
K. K. Chawla, C. Coffin, and Z. R. Xu, “Interface Engineering in Oxide Fibre/Oxide Matrix Composites,” International Materials Reviews, vol. 45, no. 5, pp. 165-189, 2000.
D. B. Marshall, R. F. Davis, P. E. D. Morgan, and J. R. Porter, “Interface Materials for Damage-Tolerant Oxide Composites,” Key Engineering Materials, vol. 127-131, pp. 27-36, November 1996.
J. P. Singh, D. Singh, and M. Sutaria, “Ceramic Composites: Roles of Fiber and Interface,” Composites Part A: Applied Science and Manufacturing, vol. 30, no. 4, pp. 445-450, April 1999.
A. G. Evans and D. B. Marshall, “Overview No. 85 the Mechanical Behavior of Ceramic Matrix Composites,” Acta Metallurgica, vol. 37, no. 10, pp. 2567-2583, October 1989.
M. Shioya, S. Yasui, and A. Takaku, “Relation Between Interfacial Shear Strength and Tensile Strength of Carbon Fiber/Resin Composite Strands,” Composite Interfaces, vol. 6, no. 4. pp. 305-323, 1998.
B. A. Budiman, F. B. Juangsa, M. Aziz, I. P. Nurprasetio, and I. N. Zaini, “Experimental Verification of Interfacial Strength Effect on the Mechanical Properties of Carbon Fiber-Epoxy Composite,” International Journal on Advanced Science, Engineering and Information Technology, vol. 7, no. 6, pp. 2226-2231, 2017.
B. A. Budiman, K. Takahashi, K. Inaba, and K. Kishimoto, “A New Method of Evaluating Interfacial Properties of a Fiber/Matrix Composite,” Journal of Composite Materials, vol. 49, no. 4, pp. 465-475, February 2015.
B. A. Budiman, F. Adziman, P. L. Sambegoro, I. P. Nurprasetio, R. Ilhamsyah, and M. Aziz, “The Role of Interfacial Rigidity to Crack Propagation Path in Fiber Reinforced Polymer Composite,” Fibers and Polymers, vol. 19, no. 9, pp. 1980-1988, September 2018.
P. Baranitharan and G. Mahesh, “Alkali Treated Maize Fibers Reinforced with Epoxy Poly Matrix Composites,” International Journal of Innovative Science and Modern Engineering (IJISME), vol. 2, no. 5, pp. 1-7, April 2014.
A. Workiye and E. Woldsenbet, “Development of Maize Stalk Cellulose Fiber Reinforced Calcined Kaolinite Clay Geopolymer Composite,” Proceedings of Engineering and Technology Innovation, vol. 16, pp. 30-38, August 2020.
L. Kljajević, M. Nenadović, M. Ivanović, D. Bučevac, M. Mirković, N. M. Nikolić, et al., “Heat Treatment of Geopolymer Samples Obtained by Varying Concentration of Sodium Hydroxide as Constituent of Alkali Activator,” Gels, vol. 8, no. 6, article no. 333, June 2022.
L. Chen, Z. Wang, Y. Wang, and J. Feng, “Preparation and Properties of Alkali Activated Metakaolin-Based Geopolymer,” Materials (Basel), vol. 9, no. 9, article no. PMC5457102, September 2016.
H. Kamarudin, A. M. M. A. Bakri, M. Binhussain, C. M. Ruzaidi, M. Luqman, C. Y. Heah, et al., “Preliminary Study on Effect of NaOH Concentration on Early Age Compressive Strength of Kaolin-Based Green Cement,” International Conference on Chemistry and Chemical Process, vol. 10, pp. 18-24, 2011.
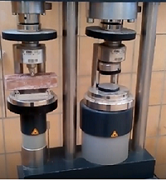
Published
How to Cite
Issue
Section
License
Copyright (c) 2023 Addisu Workiye, Eyassu Woldesenbet

This work is licensed under a Creative Commons Attribution-NonCommercial 4.0 International License.
Submission of a manuscript implies: that the work described has not been published before that it is not under consideration for publication elsewhere; that if and when the manuscript is accepted for publication. Authors can retain copyright of their article with no restrictions. Also, author can post the final, peer-reviewed manuscript version (postprint) to any repository or website.
Since Oct. 01, 2015, PETI will publish new articles with Creative Commons Attribution Non-Commercial License, under The Creative Commons Attribution Non-Commercial 4.0 International (CC BY-NC 4.0) License.
The Creative Commons Attribution Non-Commercial (CC-BY-NC) License permits use, distribution and reproduction in any medium, provided the original work is properly cited and is not used for commercial purposes