CAE Analysis of Secondary Shaft Systems in Great Five-axis Turning-Milling Complex CNC Machine
Keywords:
CAE, static analysis, linear analysis, SOLIDWORKS, shaft systems, stress analysis, CNCAbstract
The commercial computer aided engineering (CAE) software is used to analyze the linear-static construction, stress and deformation for the secondary shaft systems in great five-axis turning-milling complex computer numerical control (CNC) machine. It is convenient and always only three dimensional (3D) graphic parts needed firstly prepared and further more detail used for the commercial CAE. It is desirable to predict a deformed position for the cut tool under external pressure loads in the working process of CNC machine. The linear results for static analysis of stresses, displacements in corresponding to the screw shaft locates at top, medium and bottom positions of the secondary shaft systems are obtained by using the simulation module of SOLIDWORKS®.
References
A. Afkhamifar, D. Antonelli, and P. Chiabert, “Variational analysis for CNC milling process,” Procedia CIRP, vol. 43, pp. 118-123, 2016.
A. Max, V. Lašová, and Š. Pušman, “Enhancement of teaching design of CNC milling machines,” Procedia - Social and Behavioral Sciences, vol. 176, pp. 571-577, 2015.
Y. Altintas, P. Kersting, D. Biermann, E. Budak, B. Denkena, and I. Lazoglu, “Virtual process systems for part machining operations,” CIRP Annals - Manufacturing Technology, vol. 63, no. 2, pp. 585-605, 2014.
M. Soori, B. Arezoo, and M. Habibi, “Virtual machining considering dimensional, geometrical and tool deflection errors in three-axis CNC milling machines,” Journal of Manufacturing Systems, vol. 33, no. 4, pp. 498-507, 2014
K. H. Chang, “Chapter 2 - virtual machining,” in Product Manufacturing and Cost Estimating Using Cad/Cae, pp. 39-93, 2013.
Y. Wang, B. Cui, K. Li, T. Zhang, and Z. Zhang, “Structural analysis and experimental research of an CNC hydraulic swing-type plate shears,” AASRI Procedia, vol. 3, pp. 414-420, 2012.
A. MacKrell, “Multiscale composite analysis in Abaqus: theory and motivations,” Reinforced Plastics, 2016.
R. M. F. Paulo, F. Teixeira-Dias, and R. A. F. Valente, “Numerical simulation of aluminium stiffened panels subjected to axial compression: sensitivity analyses to initial geometrical imperfections and material properties,” Thin-Walled Structures, vol. 62, pp. 65-74, 2013.
W. Younis, “Chapter 15 - DP13 - assembly optimization: structural optimization of a lifting mechanism,” Up and running with Autodesk Inventor simulation 2011 (Second edition) A step-by-step guide to engineering design solutions, pp. 353-372, available online 26 May 2010.
C. C. Hong, C. L. Chang, and C. Y. Lin, “Static structural analysis of great five-axis turning-milling complex CNC machine,” Engineering Science and Technology, an International Journal, vol. 19, no. 4, pp. 1971-1984, 2016.
C. Yang, Z. Liqiang, and L. Dong, “General stiffness model for five-axis CNC machining,” International Journal of Research in Engineering and Science, vol. 3, no. 8, pp. 43-47, 2015.
E. Wagner, “A new optimization CAD/CAM/CAE technique for the processing of the complex 3D surfaces on 5 Axes CNC machines,” Procedia Technology, vol. 19, pp. 34-39, 2015.
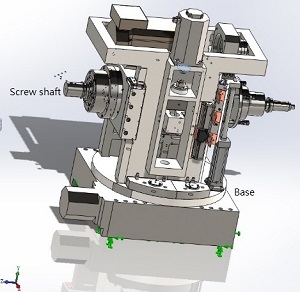
Published
How to Cite
Issue
Section
License
Submission of a manuscript implies: that the work described has not been published before that it is not under consideration for publication elsewhere; that if and when the manuscript is accepted for publication. Authors can retain copyright in their articles with no restrictions. is accepted for publication. Authors can retain copyright of their article with no restrictions.
Since Jan. 01, 2019, AITI will publish new articles with Creative Commons Attribution Non-Commercial License, under The Creative Commons Attribution Non-Commercial 4.0 International (CC BY-NC 4.0) License.
The Creative Commons Attribution Non-Commercial (CC-BY-NC) License permits use, distribution and reproduction in any medium, provided the original work is properly cited and is not used for commercial purposes.