Optimization of Centrifugal Pump Based on Impeller-Volute Interactions
DOI:
https://doi.org/10.46604/aiti.2022.8509Keywords:
centrifugal pump, optimization, design of experiment, experimental analysis, numerical analysisAbstract
The design and off-design performance of a centrifugal pump largely depends on geomechanical parameters. This study aims at enhancing the performance by optimizing three geomechanical parameters of impeller-volute interactions. The present optimization is carried out using the Taguchi method combined with a numerical approach. A comparison between the base and optimized pumps is presented under the design and off-design conditions based on numerical and experimental analyses. The numerical results reveal that, compared to the base pump, the optimized pump shows the improved performance through uniform pressure distribution in the impeller, the reduced low-pressure region towards a blade’s leading edge, and the stable total pressure at the impeller-volute interaction zone. The experimental results suggest that the optimized pump covers a wider range of operation, and its best efficiency point (BEP) is 10%, 5%, and 12% higher in flow rate, head, and efficiency, as compared to the base one.
References
G. Peng, S. Hong, H. Chang, Z. Zhang, and F. Fan, “Optimization Design of Multistage Pump Impeller Based on Response Surface Methodology,” Journal of Theoretical and Applied Mechanics, vol. 59, no. 4, pp. 595-609, 2021.
S. H. Susilo and A. Setiawan, “Analysis of the Number and Angle of the Impeller Blade to the Performance of Centrifugal Pump,” EUREKA: Physics and Engineering, vol. 2021, no. 5, pp. 62-68, September 2021.
G. R. A. Elyamin, M. A. Bassily, K. Y. Khalil, and M. S. Gomaa, “Effect of Impeller Blades Number on the Performance of a Centrifugal Pump,” Alexandria Engineering Journal, vol. 58, no. 1, pp. 39-48, March 2019.
B. Shi, K. Zhou, J. Pan, X. Zhang, R. Ying, L. Wu, et al., “PIV Test of the Flow Field of a Centrifugal Pump with Four Types of Impeller Blades,” Journal of Mechanics, vol. 37, pp. 192-204, 2021.
S. A. I. Bellary and A. Samad, “Improvement of Efficiency by Design Optimization of a Centrifugal Pump Impeller,” Proc. of ASME Turbo Expo: Turbine Technical Conference and Exposition, pp. 1-11, June 2014.
D. Wu, P. Yan, X. Chen, P. Wu, and S. Yang, “Effect of Trailing-Edge Modification of a Mixed-Flow Pump,” Journal of Fluids Engineering, vol. 137, no. 10, 101205, October 2015.
Y. Zhang, S. Hu, J. Wu, Y. Zhang, and L. Chen, “Multi-Objective Optimization of Double Suction Centrifugal Pump Using Kriging Metamodels,” Advance in Engineering Software, vol. 74, pp. 16-26, August 2014.
S. Derakhshan and N. Kasaeian, “Optimization, Numerical, and Experimental Study of a Propeller Pump as Turbine,” Journal of Energy Resources Technology, vol. 136, no. 1, 012005, March 2014.
Y. Xu, L. Tan, S. Cao, and W. Qu, “Multiparameter and Multiobjective Optimization Design of Centrifugal Pump Based on Orthogonal Method,” Proc. of the Institution of Mechanical Engineers, Part C: Journal of Mechanical Engineering Science, vol. 231, no. 14, pp. 2569-2579, July 2017.
Z. Li, H. Ding, X. Shen, and Y. Jiang, “Performance Optimization of High Specific Speed Centrifugal Pump Based on Orthogonal Experiment Design Method,” Processes, vol. 7, no. 10, 728, October 2019.
Y. Sekino and H. Watanabe, “Design Optimization of Double-Suction Volute Pumps,” World Pumps, vol. 2016, no. 5, pp. 32-35, May 2016.
J. H. Kim, B. M. Cho, Y. S. Kim, Y. S. Choi, K. Y. Kim, J. H. Kim, et al., “Optimization of a Single-Channel Pump Impeller for Wastewater Treatment,” International Journal of Fluid Machinery and Systems, vol. 9, no. 4, pp. 370-381, October-December 2016.
D. O. Baun and R. D. Flack, “Effects of Volute Design and Number of Impeller Blades on Lateral Impeller Forces and Hydraulic Performance,” International Journal of Rotating Machinery, vol. 9, no. 2, pp. 145-152, 2003.
A. J. Stepanoff, Centrifugal and Axial Flow Pumps: Theory, Design, and Application, Florida: Krieger Publishing Company, 1993.
H. Alemi, S. A. Nourbakhsh, M. Raisee, and A. F. Najafi, “Effects of Volute Curvature on Performance of a Low Specific-Speed Centrifugal Pump at Design and Off-Design Conditions,” Journal of Turbomachinery, vol. 137, no. 4, 041009, April 2015.
C. Wang, Y. Zhang, H. Hou, Z. Yuan, and M. Liu, “Optimization Design of an Ultra-Low Specific-Speed Centrifugal Pump Using Entropy Production Minimization and Taguchi Method,” International Journal of Fluid Machinery and Systems, vol. 13, no. 1, pp. 55-67, January-March 2020.
End-Suction Centrifugal Pumps (Rating 16 Bar)—Designation, Nominal Duty Point and Dimensions, ISO 2858, 2017.
W. Wang, M. K. Osman, J. Pei, S. Yuan, J. Cao, and F. K. Osman, “Efficiency-House Optimization to Widen the Operation Range of the Double-Suction Centrifugal Pump,” Complexity, vol. 2020, 9737049, 2020.
A. F. Ayad, H. M. Abdalla, and A. A. E. A. Aly, “Effect of Semi-Open Impeller Side Clearance on the Centrifugal Pump Performance Using CFD,” Aerospace Science and Technology, vol. 47, pp. 247-255, December 2015.
M. Jeon, T. T. Nguyen, H. K. Yoon, and H. J. Cho, “A Study on Verification of the Dynamic Modeling for a Submerged Body Based on Numerical Simulation,” International Journal of Engineering and Technology Innovation, vol. 10, no. 2, pp. 107-120, March 2020.
J. F. Gülich, Centrifugal Pumps, New York: Springer, 2008.
Rotodynamic Pumps—Hydraulic Performance Acceptance Tests—Grades 1 and 2, ISO 9906, 2012.
S. Kline and F. Mcclintock, “Describing Uncertainties in Single-Sample Experiments,” Mechanical Engineering, vol. 75, pp. 3-8, 1953.
W. Wang, Y. Li, M. K. Osman, S. Yuan, B. Zhang, and J. Liu, “Multi-Condition Optimization of Cavitation Performance on a Double-Suction Centrifugal Pump Based on ANN and NSGA-II,” Processes, vol. 8, no. 9, 1124, September 2020.
G. Hongyu, J. Wei, W. Yuchuan, T. Hui, L. Ting, and C. Diyi, “Numerical Simulation and Experimental Investigation on the Influence of the Clocking Effect on the Hydraulic Performance of the Centrifugal Pump as Turbine,” Renewable Energy, vol. 168, pp. 21-30, May 2021.
X. Li, B. Chen, X. Luo, and Z. Zhu, “Effects of Flow Pattern on Hydraulic Performance and Energy Conversion Characterisation in a Centrifugal Pump,” Renewable Energy, vol. 151, pp. 475-487, May 2020.
R. Tao, X. Zhao, and Z. Wang, “Evaluating the Transient Energy Dissipation in a Centrifugal Impeller under Rotor-Stator Interaction,” Entropy, vol. 21, no. 3, 271, March 2019.
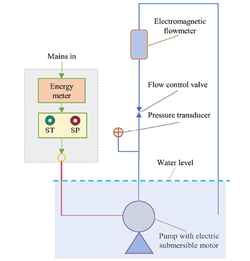
Published
How to Cite
Issue
Section
License
Submission of a manuscript implies: that the work described has not been published before that it is not under consideration for publication elsewhere; that if and when the manuscript is accepted for publication. Authors can retain copyright in their articles with no restrictions. is accepted for publication. Authors can retain copyright of their article with no restrictions.
Since Jan. 01, 2019, AITI will publish new articles with Creative Commons Attribution Non-Commercial License, under The Creative Commons Attribution Non-Commercial 4.0 International (CC BY-NC 4.0) License.
The Creative Commons Attribution Non-Commercial (CC-BY-NC) License permits use, distribution and reproduction in any medium, provided the original work is properly cited and is not used for commercial purposes.