Maintenance Initiation Prediction Incorporating Vibrations and System Availability
DOI:
https://doi.org/10.46604/aiti.2022.8618Keywords:
availability, condition-based maintenance, alert limit, alarm limit, acceleration factorAbstract
As per ISO-10816, electric motors up to 15 kW are classified as Class I machines, and the major reason for their failure is that the vibrations in them are above the alert limit. This study presents a new model for predicting the condition-based maintenance (CBM) initiation points through vibration measurement in a system of Class I machines. The proposed model follows the accelerated life testing (ALT) procedure. ALT includes the formation of an artificial wear environment in bearings to analyze the resultant system vibrations on system availability. The artificial wear environment created is close to the real industrial situation. The results show that the prediction of the CBM initiation points is based on the established relation between the system availability and vibrations. Furthermore, a relation between the available time for maintenance initiation and different vibration velocities is demonstrated.
References
H. D. Goel, J. Grievink, P. M. Herder, and M. P. Weijnen, “Integrating Reliability Optimization into Chemical Process Synthesis,” Reliability Engineering and System Safety, vol. 78, no. 3, pp. 247-258, December 2002.
S. S. Rao, Reliability-Based Design, 1st ed., New York: McGraw-Hill Inc., 1992.
R. Gulati, Maintenance and Reliability Best Practices, 2nd ed., New York: Industrial Press Inc., 2012.
Y. Li, S. Peng, Y. Li, and W. Jiang, “A Review of Condition-Based Maintenance: Its Prognostic and Operational Aspects,” Frontiers of Engineering Management, vol. 7, no. 5, pp. 323-334, July 2020.
J. H. Shin and H. B. Jun, “On Condition Based Maintenance Policy,” Journal of Computational Design and Engineering, vol. 2, no. 2, pp. 119-127, January 2015.
A. A. Manjare and B. G. Patil, “A Review: Condition Based Techniques and Predictive Maintenance for Motor,” International Conference on Artificial Intelligence and Smart Systems, pp. 807-813, March 2021.
S. Kumar, D. Mukherjee, P. K. Guchhait, R. Banerjee, A. K. Srivastava, D. N. Vishwakarma, et al., “A Comprehensive Review of Condition Based Prognostic Maintenance (CBPM) for Induction Motor,” IEEE Access, vol. 7, pp. 90690-90704, July 2019.
A. R. Mohanty, Machinery Condition Monitoring: Principles and Practices, 1st ed., USA: CRC Press, 2014.
R. K. Mobley, Root Cause Failure Analysis, 1st ed., Burlington: Elsevier, 1999.
A. Bianchini, J. Rossi, and L. Antipodi, “A Procedure for Condition-Based Maintenance and Diagnostics of Submersible Well Pumps through Vibration Monitoring,” International Journal of System Assurance Engineering and Management, vol. 9, no. 3, pp. 999-1013, February 2018.
S. K. S. A. Adawi and G. R. Rameshkumar, “Vibration Diagnosis Approach for Industrial Gas Turbine and Failure Analysis,” British Journal of Applied Science and Technology, vol. 14, no. 2, pp. 1-9, January 2016.
S. Pattabhiraman, G. Levesque, N. H. Kim, and N. K. Arakere, “Uncertainty Analysis for Rolling Contact Fatigue Failure Probability of Silicon Nitride Ball Bearings,” International Journal of Solids and Structures, vol. 47, no. 18-19, pp. 2543-2553, September 2010.
V. B. Bhandari, Design of Machine Elements, 4th ed., New Delhi: McGraw Hill Education India Private Limited, 2017.
R. K. Upadhyay, L. A. Kumaraswamy, and M. S. Azam, “Rolling Element Bearing Failure Analysis: A Case Study,” Case Studies in Engineering Failure Analysis, vol. 1, no. 1, pp. 15-17, January 2013.
S. Kulkarni and S. B. Wadkar, “Experimental Investigation for Distributed Defects in Ball Bearing Using Vibration Signature Analysis,” Procedia Engineering, vol. 144, pp. 781-789, December 2016.
C. Zhang, I. Chuckpaiwong, S. Y. Liang, and B. B. Seth, “Mechanical Component Lifetime Estimation Based on Accelerated Life Testing with Singularity Extrapolation,” Mechanical Systems and Signal Processing, vol. 16, no. 4, pp. 705-718, July 2002.
J. B. Bernstein, Reliability Prediction from Burn-In Data Fit to Reliability Models, 1st ed., London: Elsevier, 2014.
NIST/SEMATECH, “Engineering Statistics Handbook,” https://www.itl.nist.gov/div898/handbook/ April 2012.
M. Vishwakarma, R. Purohit, V. Harshlata, and P. Rajput, “Vibration Analysis and Condition Monitoring for Rotating Machines: A Review,” Materials Today: Proceedings, vol. 4, no. 2, pp. 2659-2664, December 2017.
A. Boum, N. Y. J. Maurice, L. N. Nneme, and L. M. Mbumda, “Fault Diagnosis of an Induction Motor Based on Fuzzy Logic, Artificial Neural Network and Hybrid System,” International Journal of Control Science and Engineering, vol. 8, no. 2, pp. 42-51, August 2018.
B. K. P. Kumar, Y. Basavaraj, M. J. Sandeep, and N. K. Kumar, “Optimization of Process Parameters for Turning Machine Using Taguchi Super Ranking Method: A Case Study in Valve Industry,” Materials Today: Proceedings, vol. 47, no. 10, pp. 2505-2508, May 2021.
A. Coppe, M. J. Pais, R. T. Haftka, and N. H. Kim, “Using a Simple Crack Growth Model in Predicting Remaining Useful Life,” Journal of Aircraft, vol. 49, no. 6, pp. 1965-1973, November 2012.
Z. Kang, C. Catal, and B. Tekinerdogan, “Remaining Useful Life (RUL) Prediction of Equipment in Production Lines Using Artificial Neural Networks,” Sensors, vol. 21, no. 3, Article no. 932, January 2021.
X. Han, Z. Wang, M. Xie, Y. He, Y. Li, and W. Wang, “Remaining Useful Life Prediction and Predictive Maintenance Strategies for Multi-State Manufacturing Systems Considering Functional Dependence,” Reliability Engineering and System Safety, vol. 210, no. 11, Article no. 107560, June 2021.
E. Quatrini, F. Costantino, G. D. Gravio, and R. Patriarca, “Condition-Based Maintenance—An Extensive Literature Review,” Machines, vol. 8, no. 2, Article no. 31, June 2020.
A. J. Bazurto, E. C. Quispe, and R. C. Mendoza, “Causes and Failures Classification of Industrial Electric Motor,” IEEE ANDESCON, pp. 1-4, October 2016.
R. Karakolev and L. Dimitrov, “Analysis of Electrical Motor Mechanical Failures Due to Bearings,” IOP Conference Series: Materials Science and Engineering, vol. 393, no. 1, Article no. 012064, August 2018.
G. K. Nikas, “A State-of-the-Art Review on the Effects of Particulate Contamination and Related Topics in Machine-Element Contacts,” Proceedings of the Institution of Mechanical Engineers, Part J: Journal of Engineering Tribology, vol. 224, no. 5, pp. 453-479, March 2010.
A. Regattieri, F. Piana, M. Gamberi, F. G. Galizia, and A. Casto, “Reliability Assessment of a Packaging Automatic Machine by Accelerated Life Testing Approach,” Procedia Manufacturing, vol. 11, pp. 2178-2186, January 2017.
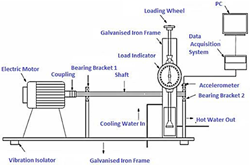
Published
How to Cite
Issue
Section
License
Submission of a manuscript implies: that the work described has not been published before that it is not under consideration for publication elsewhere; that if and when the manuscript is accepted for publication. Authors can retain copyright in their articles with no restrictions. is accepted for publication. Authors can retain copyright of their article with no restrictions.
Since Jan. 01, 2019, AITI will publish new articles with Creative Commons Attribution Non-Commercial License, under The Creative Commons Attribution Non-Commercial 4.0 International (CC BY-NC 4.0) License.
The Creative Commons Attribution Non-Commercial (CC-BY-NC) License permits use, distribution and reproduction in any medium, provided the original work is properly cited and is not used for commercial purposes.