Metallurgical Characterization of SS 316L Repurposed by Wire Plus Arc Additive Manufacturing
DOI:
https://doi.org/10.46604/ijeti.2023.11417Keywords:
wire plus arc additive manufacturing, repurposing, 316L, metallurgical characterizationAbstract
This research aims to analyze the microstructures and mechanical characteristics of stainless steel (SS) 316L repurposed by wire plus arc additive manufacturing (WAAM). The SS 316L wire is deposited on a SS 316 substrate, which can be repurposed. This deposited material underwent optical microscopy, X-ray diffraction, and tensile test, and the results indicate that it features cellular and columnar dendrites at the bottom and equiaxial grains at the top. The tensile strength of the interface region between the deposited material (DM) and the base material (BM) is the highest (559 ± 4.16 MPa vs. 510 ± 4.93 MPa in DM and 540 ± 2.65 in BM), indicating that the BM and the deposited layers are strongly bonded. All the results from the defect observation, microstructures, and mechanical characteristics confirm the potential of the WAAM process for repurposing.
References
S. W. Williams, F. Martina, A. C. Addison, J. Ding, G. Pardal, and P. Colegrove, “Wire + Arc Additive Manufacturing,” Materials Science and Technology, vol. 32, no. 7, pp. 641-647, 2016.
V. T. Le, D. S. Mai, V. T. Dang, D. M. Dinh, T. H. Cao, and V. A. Nguyen, “Optimization of Weld Parameters in Wire and Arc-Based Directed Energy Deposition of High Strength Low Alloy Steels,” Advances in Technology Innovation, vol. 8, no. 1, pp. 01-11, January 2023.
V. T. Le, H. Paris, and G. Mandil, “Process Planning for Combined Additive and Subtractive Manufacturing Technologies in a Remanufacturing Context,” Journal of Manufacturing Systems, vol. 44, no. 1, pp. 243-254, July 2017.
P. Artie Gene Jr., D. W. Gandy, G. J. Frederick, J. T. Stover, and R. Viswanathan, Method and Apparatus for Repairing Superalloy Components, U.S. Patent, 6,673,169 B1, January 04, 2004.
S. Zhu, “Robotic GMAW Forming Remanufacturing Technology,” Advances in Manufacturing, vol. 1, no. 1, pp. 87-90, March 2013.
X. Hong, G. Xiao, Y. Zhang, and J. Zhou, “Research on Gradient Additive Remanufacturing of Ultra-Large Hot Forging Die Based on Automatic Wire Arc Additive Manufacturing Technology,” The International Journal of Advanced Manufacturing Technology, vol. 116, no. 7-8, pp. 2243-2254, October 2021.
Y. Li, Q. Han, I. Horváth, and G. Zhang, “Repairing Surface Defects of Metal Parts by Groove Machining and Wire + Arc Based Filling,” Journal of Materials Processing Technology, vol. 274, article no. 116268, December 2019.
J. H. Lee, C. M. Lee, and D. H. Kim, “Repair of Damaged Parts Using Wire Arc Additive Manufacturing in Machine Tools,” Journal of Materials Research and Technology, vol. 16, pp. 13-24, January-February 2022.
P. C. Priarone, G. Campatelli, A. R. Catalano, and F. Baffa, “Life-Cycle Energy and Carbon Saving Potential of Wire Arc Additive Manufacturing for the Repair of Mold Inserts,” CIRP Journal of Manufacturing Science and Technology, vol. 35, pp. 943-958, November 2021.
V. T. Le and H. Paris, “On the Use of Gas-Metal-Arc-Welding Additive Manufacturing for Repurposing of Low-Carbon Steel Components: Microstructures and Mechanical Properties,” Welding in the World, vol. 65, no. 1, pp. 157-166, January 2021.
W. Jin, C. Zhang, S. Jin, Y. Tian, D. Wellmann, and W. Liu, “Wire Arc Additive Manufacturing of Stainless Steels: A Review,” Applied Sciences, vol. 10, no. 5, article no. 1563, March 2020.
V. T. Le, H. Paris, and G. Mandil, “The Development of a Strategy for Direct Part Reuse Using Additive and Subtractive Manufacturing Technologies,” Additive Manufacturing, vol. 22, pp. 687-699, August 2018.
V. T. Le, H. Paris, and G. Mandil, “Environmental Impact Assessment of an Innovative Strategy Based on an Additive and Subtractive Manufacturing Combination,” Journal of Cleaner Production, vol. 164, pp. 508-523, October 2017.
A. M. King, S. C. Burgess, W. Ijomah, and C. A. McMahon, “Reducing Waste: Repair, Recondition, Remanufacture or Recycle?” Sustainable Development, vol. 14, no. 4, pp. 257-267, October 2006.
X. Wang and K. Chou, “The Effects of Stress Relieving Heat Treatment on the Microstructure and Residual Stress of Inconel 718 Fabricated by Laser Metal Powder Bed Fusion Additive Manufacturing Process,” Journal of Manufacturing Processes, vol. 48, pp. 154-163, December 2019.
F. W. C. Farias, J. da Cruz Payão Filho, and V. H. P. M. e Oliveira, “Prediction of the Interpass Temperature of a Wire Arc Additive Manufactured Wall: FEM Simulations and Artificial Neural Network,” Additive Manufacturing, vol. 48, no. A, article no. 102387, December 2021.
B. Q. Chen, M. Hashemzadeh, and C. Guedes Soares, “Numerical and Experimental Studies on Temperature and Distortion Patterns in Butt-Welded Plates,” The International Journal of Advanced Manufacturing Technology, vol. 72, no. 5-8, pp. 1121-1131, May 2014.
J. Ding, P. Colegrove, J. Mehnen, S. Ganguly, P. M. Sequeira Almeida, F. Wang, et al., “Thermo-Mechanical Analysis of Wire and Arc Additive Layer Manufacturing Process on Large Multi-Layer Parts,” Computational Materials Science, vol. 50, no. 12, pp. 3315-3322, December 2011.
M. C. Bui, V. T. Le, D. X. Ta, D. S. Mai, D. M. Dinh, T. K. Doan, et al., “Thermal Analysis in Wire Arc Additively Manufactured SS308L Walls Via Numerical Simulations,” Proceedings of the International Conference on Advanced Mechanical Engineering, Automation, and Sustainable Development 2021, pp. 10-15, 2022.
J. C. Lippold and D. J. Kotecki, Welding Metallurgy and Weldability of Stainless Steels, Hoboken NJ: John Wiley, 2005.
V. T. Le, D. S. Mai, M. C. Bui, K. Wasmer, V. A. Nguyen, D. M. Dinh, et al., “Influences of the Process Parameter and Thermal Cycles on the Quality of 308L Stainless Steel Walls Produced by Additive Manufacturing Utilizing an Arc Welding Source,” Welding in the World, vol. 66, no. 8, pp. 1565-1580, August 2022.
S. H. Lee, “CMT-Based Wire Arc Additive Manufacturing Using 316L Stainless Steel: Effect of Heat Accumulation on the Multi-Layer Deposits,” Metals, vol. 10, no. 2, article no. 278, February 2020.
R. D. Willis, F. T. Blanchard, and T. L. Conner, “Guidelines for the Application of SEM/EDX Analytical Techniques to Particulate Matter Samples,” United States Environmental Protection Agency, Technical Report PB2004100988, September 2002.
P. N. Bellamkonda, M. Sudersanan, and B. Visvalingam, “Characterisation of a Wire Arc Additive Manufactured 308L Stainless Steel Cylindrical Component,” Materials Testing, vol. 64, no. 10, pp. 1397-1409, October 2022.
V. T. Le, D. S. Mai, T. K. Doan, and H. Paris, “Wire and Arc Additive Manufacturing of 308L Stainless Steel Components: Optimization of Processing Parameters and Material Properties,” Engineering Science and Technology, an International Journal, vol. 24, no. 4, pp. 1015-1026, August 2021.
K. K. Singh, S. Sangal, and G. S. Murty, “Hall–Petch Behaviour of 316L Austenitic Stainless Steel at Room Temperature,” Materials Science and Technology, vol. 18, no. 2, pp. 165-172, 2002.
M. Kerschbaumer, G. Ernst, and P. O’Leary, “Tool Path Generation for 3D Laser Cladding Using Adaptive Slicing Technology,” International Congress on Applications of Lasers & Electro-Optics, vol. 2005, article no. 604, 2005.
J. Plangger, P. Schabhüttl, T. Vuherer, and N. Enzinger, “CMT Additive Manufacturing of a High Strength Steel Alloy for Application in Crane Construction,” Metals, vol. 9, no. 6, article no. 650, June 2019.
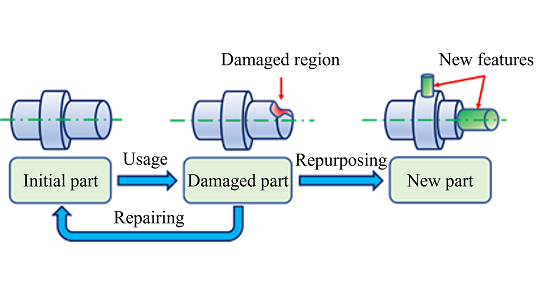
Published
How to Cite
Issue
Section
License
Copyright (c) 2023 Duong Vu, Van Thao Le

This work is licensed under a Creative Commons Attribution-NonCommercial 4.0 International License.
Copyright Notice
Submission of a manuscript implies: that the work described has not been published before that it is not under consideration for publication elsewhere; that if and when the manuscript is accepted for publication. Authors can retain copyright in their articles with no restrictions. Also, author can post the final, peer-reviewed manuscript version (postprint) to any repository or website.
Since Jan. 01, 2019, IJETI will publish new articles with Creative Commons Attribution Non-Commercial License, under Creative Commons Attribution Non-Commercial 4.0 International (CC BY-NC 4.0) License.
The Creative Commons Attribution Non-Commercial (CC-BY-NC) License permits use, distribution and reproduction in any medium, provided the original work is properly cited and is not used for commercial purposes.