Effect of Volute Collector on the Performance of Centrifugal Pump Based on Entropy Generation Analysis
DOI:
https://doi.org/10.46604/ijeti.2022.9741Keywords:
centrifugal pump, entropy production, energy loss, volute collectorAbstract
A proper design of centrifugal pumps reduces power loss and improves efficiency. This study aims to investigate and analyze the effect of different volute collector configurations on centrifugal pump performance. Locations of losses are detected using the entropy production rate, whereas the number of losses is evaluated using user-defined codes. Three volute collectors are selected based on their connections with standard pipes. A steady flow numerical analysis is performed to determine the performance parameters of the centrifugal pump and select a modified volute collector design. Comparing the results of experiments on the base and modified volute collectors confirmed that the proper design of the volute collector can help reduce the secondary flow losses at subsequent locations, which reduces the entropy production and losses. As compared to the base pump, the modified volute collector improved the pump efficiency by 3% at the duty flow.
References
C. Wang W. D. Shi, X. K. Wang, X. P. Jiang, Y. Yang, W. Li, et al., “Optimal Design of Multistage Centrifugal Pump Based on the Combined Energy Loss Model and Computational Fluid Dynamics,” Applied Energy, vol. 187, pp. 10-26, February 2017.
Y. Hao and L. Tan, “Symmetrical and Unsymmetrical Tip Clearances on Cavitation Performance and Radial Force of a Mixed Flow Pump as Turbine at Pump Mode,” Renewable Energy, vol. 127, pp. 368-376, April 2018.
F. Kock and H. Herwig, “Entropy Production Calculation for Turbulent Shear Flows and their Implementation in CFD Codes,” International Journal of Heat and Fluid Flow, vol. 26, no. 4, pp. 672-680, June 2005.
M. Bhole, C. Ford, and J. Bennington, “Characterization of Axial Flow Impellers in Pulp Fibre Suspensions,” Chemical Engineering Research and Design, vol. 87, pp. 648-653, April 2009.
G. Hongyu, J. Wei, W. Yuchuan, T. Hui, L. Ting, and C. Diyi, “Numerical Simulation and Experimental Investigation on the Influence of the Clocking Effect on the Hydraulic Performance of the Centrifugal Pump as Turbine,” Renewable Energy, vol. 168, pp. 21-30, 2021.
Y. D. Gu, J. Pei, S. Q. Yuan, W. J. Wang, F. Zhang, P. Wang, et al., “Clocking Effect of Vaned Diffuser on Hydraulic Performance of High-Power Pump by using the Numerical Flow Loss Visualization Method,” Energy, vol. 170, pp. 986-997, March 2019.
H. Guan, W. Jiang, J. Yang, Y. Wang, X. Zhao, and J. Wang, “Energy Loss Analysis of the Double-Suction Centrifugal Pump Under Different Flow Rates Based on Entropy Production Theory,” Proceedings of the Institution of Mechanical Engineers, Part C: Journal of Mechanical Engineering Science, vol. 234, no. 20, pp. 4009-4023, April 2020.
Q. Deng, J. Pei, W. Wang, B. Lin, C. Zhang, and J. Zhao, “Energy Loss and Radial Force Variation Caused by Impeller Trimming in a Double-Suction Centrifugal Pump,” Entropy, vol. 23, no. 9, article no. 1228, September 2021.
F. Zhang, D. Appiah, F. Hong, J. F. Zhang, S. Q. Yuan, K. A. Adu-Poku, et al., “Energy Loss Evaluation in a Side Channel Pump under Different Wrapping Angles using Entropy Production Method,” International Communications in Heat and Mass Transfer, vol. 113, article no. 104526, April 2020.
P. Huang, D. Appiah, K. Chen, F. Zhang, P. Cao, and Q. Hong, “Energy Dissipation Mechanism of a Centrifugal Pump with Entropy Generation Theory,” AIP Advances, vol. 11, no. 4, article no. 045208, April 2021.
G. J. Peng, J. L. Du, H. Chang, Q. Chen, J. H. Li, C. X. Pan, et al., “Numerical and Experimental Analysis of Influence of Impeller Structures on Slurry Pump Performance,” Frontiers in Energy Research, vol. 9, article no. 762159, November 2021.
F. Yang, Z. B. Li, W. Z. Hu, C. Liu, D. J. Jiang, D. S. Liu, et al., “Analysis of Flow Loss Characteristics of Slanted Axial-Flow Pump Device Based on Entropy Production Theory,” Royal Society Open Science, vol. 9, no. 1, article no. rsos.211208, January 2022.
J. Li, D. Meng, and X. Qiao, “Numerical Investigation of Flow Field and Energy Loss in a Centrifugal Pump as Turbine,” Shock and Vibration, vol. 2020, article no. 8884385, 2020.
G. Yang, X. Zhao, D. Zhang, L. Geng, X. Yang, and X. Gao, “Hydraulic Components' Matching Optimization Design and Entropy Production Analysis in a Large Vertical Centrifugal Pump,” Journal of Mechanical Science and Technology, vol. 35, no. 11, pp. 5033-5048, October 2021.
B. Cui and C. Zhang, “Investigation on Energy Loss in Centrifugal Pump Based on Entropy Generation and High-Order Spectrum Analysis,” Journal of Fluids Engineering, Transactions of the ASME, vol. 142, no. 9, article no. 091205, September 2020.
L. Ji, W. Li, W. Shi, H. Chang, and Z. Yang, “Energy Characteristics of Mixed-Flow Pump Under Different Tip Clearances Based on Entropy Production Analysis,” Energy, vol. 199, article no. 117447, May 2020.
F. Kock and H. Herwig, “Local Entropy Production in Turbulent Shear Flows: A High-Reynolds Number Model with Wall Functions,” International Journal of Heat and Mass Transfer, vol. 47, no. 10-11, pp. 2205-2215, May 2004.
L. Zhou, J. W. Hang, L. Bai, Z. Krzemianowski, M, A, El-Emam, E. Yasser, et al., “Application of Entropy Production Theory for Energy Losses and Other Investigation in Pumps and Turbines: A Review,” Applied Energy, vol. 318, article no. 119211, July 2022.
M. Böhle, A. Fleder, and M. Mohr, “Study of the Losses in Fluid Machinery with the Help of Entropy,” 16th International Symposium on Transport Phenomena, and Dynamics of Rotating Machinery, April 2016.
H. Hou, Y. Zhang, and Z. Li, “A Numerical Research on Energy Loss Evaluation in a Centrifugal Pump System Based on Local Entropy Production Method,” Thermal Science, vol. 21, no. 3, pp. 1287-1299, 2017.
“User’s Guide: ANSYS CFX-Solver Theory Guide,” https://download.ansys.com/Product%20Documentation, 2022.
“User’s Guide: ANSYS CFX-Solver Modeling Guide,” https://download.ansys.com/Product%20Documentation, 2022.
C. Wang, Y. Zhang, H. Hou, J. Zhang, and C. Xu, “Entropy Production Diagnostic Analysis of Energy Consumption for Cavitation Flow in a Two-Stage LNG Cryogenic Submerged Pump,” International Journal of Heat and Mass Transfer, vol. 129, pp. 342-356, February 2019.
Geometrical Product Specifications (GPS) - Indication of Surface Texture in Technical Product Documentation, ISO 1302, 2002.
Rotodynamic Pumps - Hydraulic Performance Acceptance Tests - Grades 1 and 2, ISO 9906, 2012.
S. Kline and F. Mcclintock, “Describing the Uncertainties in Single Sample Experiments,” Mechanical Engineering, vol. 75, pp. 3-8, 1953.
K. M. Srinivasan, Rotodynamic Pumps: (Centrifugal and Axial), New Age International, 2008.
M. Shah, B. Baloni, and S. Channiwala, “Optimization of Centrifugal Pump Based on Impeller-Volute Interactions,” Advances in Technology Innovation, vol. 7, no. 3, pp. 216-227, June 2022.
P. Chen, X. Li, J. Ren, and H. Jiang, “Multi-Objective Optimization of Non-Axisymmetric Contoured Endwall for Axial Turbines,” International Journal of Gas Turbine, Propulsion and Power Systems, vol. 12, no. 1, pp. 1-9, 2021.
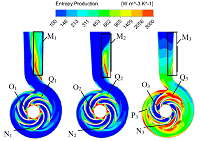
Published
How to Cite
Issue
Section
License
Copyright Notice
Submission of a manuscript implies: that the work described has not been published before that it is not under consideration for publication elsewhere; that if and when the manuscript is accepted for publication. Authors can retain copyright in their articles with no restrictions. Also, author can post the final, peer-reviewed manuscript version (postprint) to any repository or website.
Since Jan. 01, 2019, IJETI will publish new articles with Creative Commons Attribution Non-Commercial License, under Creative Commons Attribution Non-Commercial 4.0 International (CC BY-NC 4.0) License.
The Creative Commons Attribution Non-Commercial (CC-BY-NC) License permits use, distribution and reproduction in any medium, provided the original work is properly cited and is not used for commercial purposes.